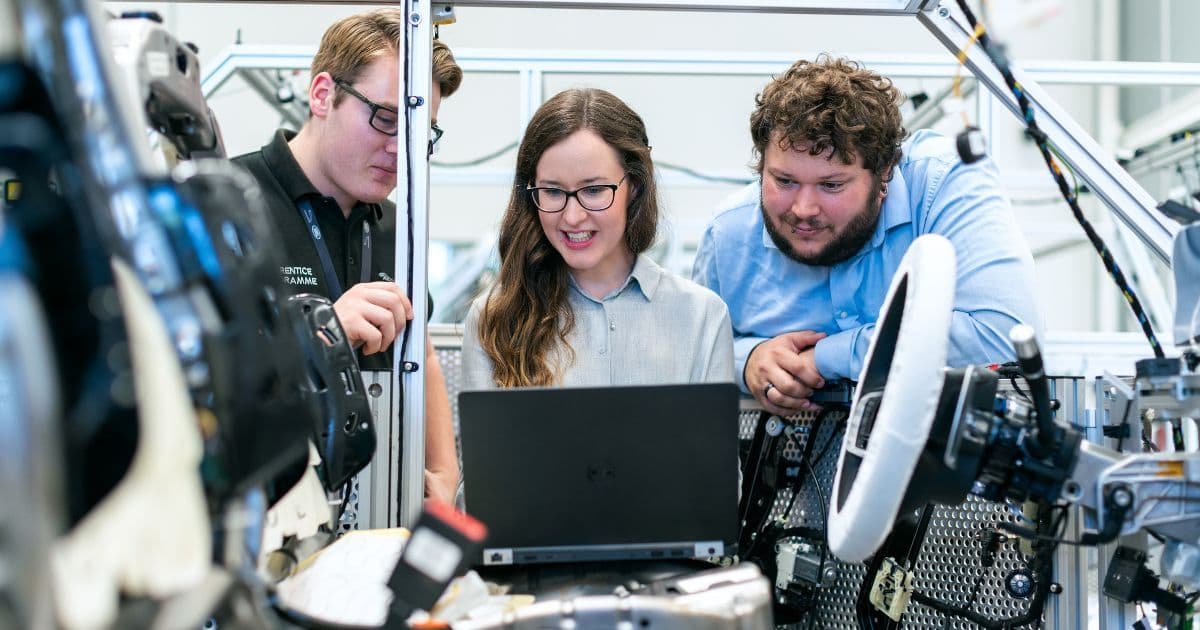

The Hidden Crisis in Engineering Education: Why Traditional Labs Aren't Enough
Standing before a $100,000 machine with an audience isn’t ideal for learning, yet it’s the reality for today’s engineering students.
Immersive. Interactive. Practical. Transformative.
Engineering students face a problem that nobody likes to talk about: most graduate without enough hands-on experience to feel confident in their skills. It's a system-wide issue that goes deeper than just limited lab hours or outdated equipment. As a former engineering student, I still remember the frustration of waiting in line to use lab equipment. Twenty of us huddled around a single CNC machine, each getting maybe 15 minutes of actual hands-on time. That's barely enough to figure out where the power button is, let alone master complex operations.
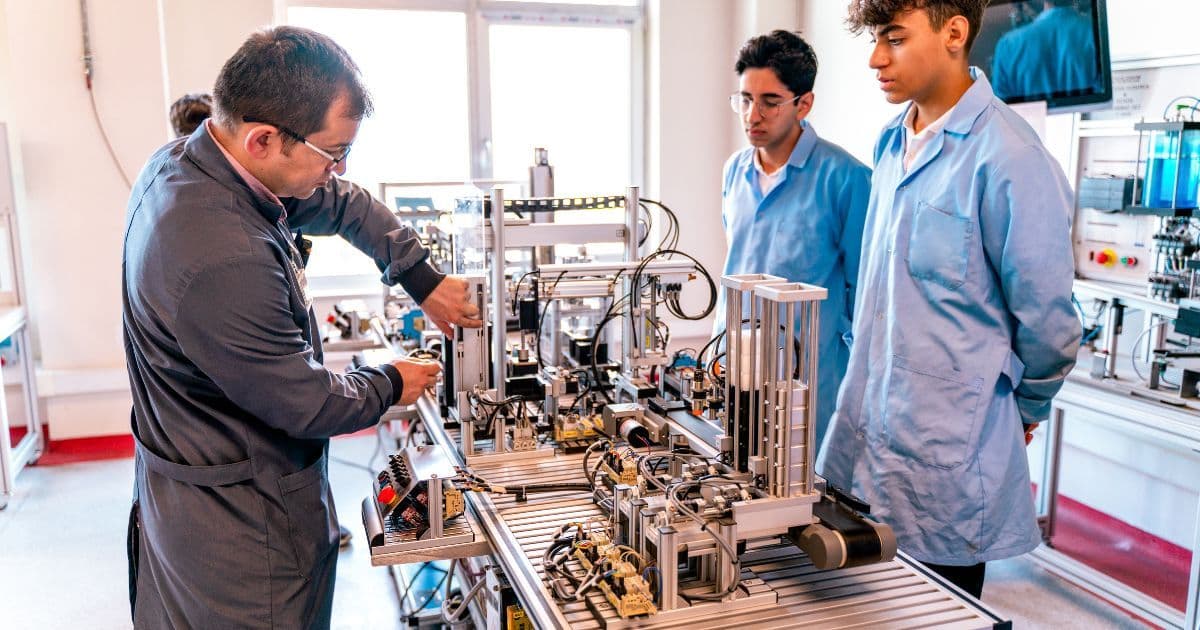
The Access Problem
Think about a typical university engineering lab. One CNC machine for 50 students. Two industrial robots shared across multiple courses. A single PCB assembly station that's always "temporarily out of order." The math simply doesn't work out:
- 3-hour lab sessions per week
- 20+ students per session
- Complex equipment that requires setup time
- Limited supervision for dangerous operations
- Expensive components that can't be wasted
Real hands-on time? Maybe 15-20 minutes per student, per week. That's assuming everything works perfectly and nothing breaks.
The Fear Factor
Here's what makes it worse: when students finally get their turn, they're terrified. Standing in front of a $100,000 piece of equipment while your professor and 20 classmates watch isn't exactly conducive to learning. Every movement is hesitant. Every decision is second-guessed. One wrong move could:
- Damage expensive equipment
- Waste limited materials
- Use up everyone else's lab time
- Create safety hazards
- Impact your grade
The Expertise Gap
Then there's the supervision problem. Even the best professors can't be everywhere at once. In a typical lab:
- One instructor manages 20+ students
- Each student needs individual guidance
- Questions go unanswered
- Mistakes go uncorrected
- Bad habits form unnoticed
The Hidden Costs
Universities are trying to solve this with more equipment, but the numbers are staggering:
- CNC Machine: $50,000 - $200,000
- Industrial Robot: $100,000+
- PCB Assembly Line: $75,000+
- Testing Equipment: $50,000+
- Annual Maintenance: 10-15% of equipment cost
- Materials and Consumables: Thousands per semester
And that's just for basic equipment. Advanced or specialized machinery? Add another zero to those numbers.
The Real-World Impact
This isn't just an academic problem. Industry leaders consistently report that new graduates:
- Lack practical experience
- Need extensive on-the-job training
- Are hesitant with equipment
- Make costly mistakes
- Take months to become productive
The gap between theoretical knowledge and practical skills isn't just frustrating - it's expensive for everyone involved.
The Traditional Solutions Aren't Working
Universities have tried various approaches:
- Extended lab hours (limited by staff availability)
- More equipment (limited by budget)
- Video demonstrations (no hands-on component)
- Computer simulations (lack physical interaction)
- Industry partnerships (limited slots available)
But none of these address the core problem: students need more time to practice, fail, learn, and build confidence.
Virtual Reality: More Than Just Another Tech Tool
This is where BlueClod comes in, but not in the way you might think. We're not just creating 3D models or simple simulations. We're building fully interactive virtual workshops where you can:
- Practice CNC programming and operation without fear of crashes
- Learn PCB assembly and testing without wasting components
- Master industrial automation systems without risk
- Experiment with different manufacturing processes
- Debug complex electrical systems safely
The key difference? You can fail. Repeatedly. And that's exactly what you need to learn.
Learning Without Limits
Think about how you actually learn technical skills. It's not from reading about them or watching videos. It's from doing, failing, adjusting, and trying again. But in traditional labs, failure is expensive and time is limited.
In our virtual workshops:
- Crash a virtual CNC machine? Reset and try again
- Blow up a circuit? Understand exactly what went wrong and restart
- Want to try a risky optimization? Go for it
- Need to practice at 2 AM before your practical exam? The workshop is always open
"But it's not the same as real equipment," you might say. You're right - and that's not our goal. We're creating a space where you can build confidence, develop muscle memory, and understand core concepts before touching real equipment.
Our platform tracks your movements with sub-millimeter precision. When you're learning to operate a lathe, for example, Adam (our AI mentor) watches every move:
- Tool angle and position
- Feed rate adjustments
- Speed control
- Safety procedures
- Emergency responses
You get instant feedback on your technique, something that's often impossible with real equipment where you might not know you've made a mistake until it's too late.
Beyond Basic Practice
But it's more than just individual practice. You can:
- Join virtual workshops with students from other universities
- Learn from industry experts who can guide you remotely
- Practice group projects without scheduling conflicts
- Access equipment your school might not have
- Track your progress with detailed analytics
I should mention that we're not trying to replace traditional engineering labs. Instead, we're solving their biggest limitations: access, practice time, and the fear of failure. When you finally get your hands on real equipment, you'll already know:
- The correct procedures
- Common pitfalls to avoid
- How to handle problems
- What good technique feels like
What's Next?
Engineering education is evolving. The days of learning purely from textbooks and limited lab time are ending. Virtual practice won't replace real-world experience, but it can help you make the most of your limited time with physical equipment.
Whether you're struggling to get enough lab time, want to practice more complex procedures, or just want to experiment without consequences, virtual training is becoming an essential part of engineering education.
Ready to transform how you learn engineering skills? Join our waitlist to be among the first to experience unlimited practice time in our virtual workshops.
Related Posts
Stay in the Loop with BlueClod
Sign up for updates on our latest VR advancements, cutting-edge features, and more.